The success of many products often resides on the impact of the environmental conditions associated with the application. Careful consideration should be given to not only the forces of an application, but also the environmental conditions. Specific combinations of conditions can result in problems such as rapid hydrolysis, discoloration, accelerated aging and cracking.
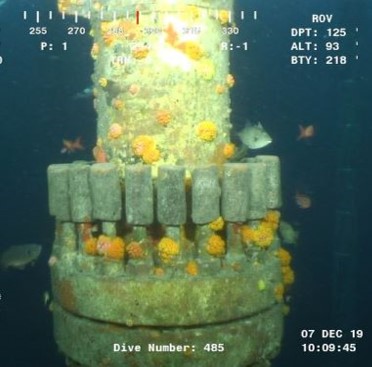
Operating Temperature
Temperature can impact all of the material’s mechanical properties. Harder parts will soften under heat and become much harder when cold, or even brittle at freezing in higher hardness materials. Excess heat will also reduce the material’s resistance to cyclic loading in dynamic applications along with its load-bearing capacity as the modulus of the material lowers when the material begins to soften.
The opposite will happen as the temperature lowers. Harder systems can become brittle in freezing conditions. The effect temperature has on the coefficient of thermal expansion can be another consideration for careful evaluation of operating temperatures.
- System Operating Temperatures
- PM1 = Medium Performance Polyether = 170F
- PP2 = Premium Performance Polyester = 170F
- PP1 = Premium Performance Polyether = 170F
- PUP1&2 = Premium Performance Polyether = 170F - 210F
- PHT1 = High-Temperature Polyether = 250F
- PUHT = Ultra-High-Temperature Polyether = 400F
- Low Temperatures
Different systems and hardnesses have different brittle points, so in applications where this is a concern, it should be reviewed to confirm the system and material meet performance requirements.
- Effect of Temperature on Modulus
Modulus will increase with a decrease in temperature, however the opposite occurs with heat, as there is a decrease in modulus as temperature increases. A harder or softer material may need to be selected so it can still meet load requirements at operating temperatures to compensate for modulus change.
- Coefficient of Thermal Expansion
If the end use of the part may be impacted by dimensional changes due to environmental conditions, then CTE analysis may be required to verify any issues which could cause performance problems in end use.
UV Exposure:
Color stabilizing additives called UV inhibitors are often needed to ensure products do not quickly change color in outdoor environments. Polyether Systems are preferred in outdoor environments as they do not break down the same way polyester systems do. Accelerated UV tests can be performed to simulate many years of product exposure and is recommended in commercial applications.
Hydrolytic Stability:
The most basic question to ask in designing a successful polyurethane product is, “Will the part wear out in 3-5 years?” If the answer is no, then a polyether is always recommended for its preferred hydrolytic stability, and in many cases, a 10 plus year shelf life.
- Hydrolytic Stability
- Polyether Systems work better in fluid based applications where desired product life cycle is beyond 3-4 years.
- Process of microbial degradation
Polyester Systems will begin to break down due to microbial degradation over time. This process is known as hydrolysis. The higher the temperature and humidity, the shorter the shelf life or usable life of the part.
Pipe Roller
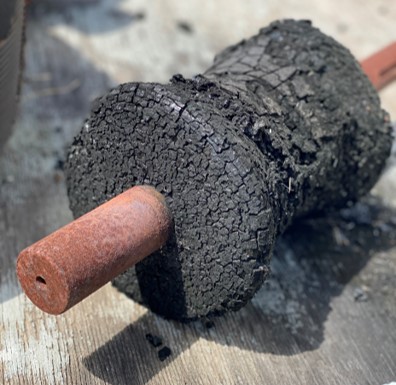
Polyester System after 7 years outdoors
Chemical Contact:
Polyurethane is resistant to a very long list of chemicals. The primary consideration for chemical contact is to determine if the parts will be continuously immersed or see intermittent use. In continuous immersion applications, we typically recommend a Polyether System if the part does not normally wear out in the application in 2 years. Polyester Systems will typically last longer in oils and solvents, if the duration is under 2 years. Fluid concentration, atmospheric exposure and temperature can also reduce the life cycle. The higher the operating temperature, the greater the impact chemicals will have on the degradation of the material.
- Chemical Contact
- Ether vs Ester
Ester Systems tend to work better in oil and solvent-based applications, however, if product failure in 2-3 years is an issue, then a High-Temperature Polyether System is recommended. This system will be more costly but will have better hydrolytic stability long term.
- Submersion vs Intermittent Contact
Parts that see intermittent contact with chemicals will last longer in submersed applications when given an opportunity to dry out. Ether Systems are typically preferred in submersed environments, given their better hydrolytic stability.
- Effects of Heat on Chemical Degradation
Heat will significantly increase the speed at which a fluid will begin to break down polyurethane. The stronger the chemical concentration and the higher the temperature, the faster the material will break down. Ultra-High-Temperature Polyether Systems are best in this application, however, there are limits to chemical concentrations and temperatures even these systems can withstand. Not every application is the same. We recommend sending us the exact chemical breakdown of a fluid, maximum operating temperature, and the duration of the worst-case conditions, so we can make a recommendation.
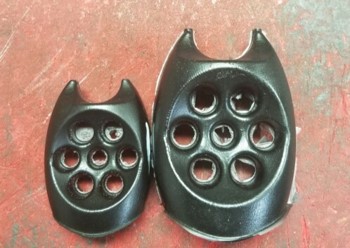
Swelling from chemical content
Both are the same part, the part on the right was soaked in solvent for 7 days to demonstrate the effect of swelling